Overview
This course will introduce to practicing engineers and analyst to lean production principles and practice. Industrial planning experts and others responsible for continuously improving operational performance must develop systems that are fast, flexible, focused and friendly for their companies, customers and production associates. The course will provide with an introduction to lean production describing the background behind its development and how evaluations and assessments of production systems are performed. Lean production tools and techniques will be described and in some cases demonstrated in simulation exercises. Issues relating to employee involvement, improvement teams, training and culture will be presented. Planning for lean process implementation and the necessity of sustain improvements will be discussed. Examples of applications in manufacturing and business processes will be presented as part of this course..
We also support you in Integrating the Deep Analysis Six sigma and lean program into your business strategy. Many companies have tried to fill the gaps in their talent and experience pools by taking this proven approach, and the results have often been astounding. The best way to approch this is to train and raise the skill of your own employees.
The duality of improvement
The two most popular process improvement methodologies in use today, lean manufacturing and Six Sigma, originated at Toyota and Motorola, respectively. These pioneering companies are discrete manufacturers. Not surprisingly, the subsequent evolution and development of these two methodologies has focused mostly on improvements in discrete manufacturing. Each methodology has a central focus that has been the basis for its structure and tools. For lean, it’s the delivery of value to the customer through the elimination of waste – anything that is non-value added from the customer’s perspective. For Six Sigma, the central focus is the elimination of defects – products or services that do not conform to the customer’s specifications.
How does Qualimations Support in lean implementation?
Process manufacturing is fundamentally different from discrete manufacturing in the way material flows. Material flows in a continuous stream in process manufacturing, while parts move in discrete batches in discrete. Since there has been so much work done in developing these methodologies in discrete manufacturing and very little in process, it might seem logical to apply them “as-is” to process-manufacturing industries. However, this approach is like trying to fit square pegs into round holes. The better approach is to adapt these techniques within a process improvement framework that identifies the various forms of waste in the process-manufacturing value stream, and manages the wastes with the appropriate concepts and tools.
What do you control by using lean concepts in your process ?
- 1 Over-production: Producing too much, too soon.
- 2 Inventory: Extra production required to buffer process variability.
- 3 Transportation: Movement of materials without adding value.
- 4 Waiting: Increasing production cycle time without adding value.
- 5 Movement: Movement of operators without adding value.
- 6 Defects: Product that does not conform to customer specifications.
- 7 Over-processing: Processing a material more than is necessary to meet customer specifications.
TPS!!!
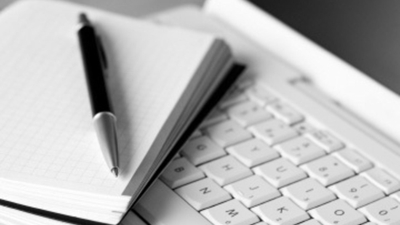
Toyota has stayed focused on its principles and not the tools. At most Toyota plants, there are no dedicated change agents or black belts. Value stream maps are rare and only used in problem areas. There are no value stream managers and only small portions of the plants contain actual standardized work charts and many of the daily tracking systems are highly computerized. For the last 50 years, “TPS at Toyota has been primarily concerned with making a profit, and satisfying the customer with the highest possible quality at the lowest cost in the shortest lead-time, while developing the talents and skills of its workforce through rigorous improvement routines and problem solving disciplines.”
This stated aim is mixed in with the twin production principles of just-in-time and jidoka (build in quality at the process).This emphasis on process improvement to obtain results rather than the implementation of tools is the main reason why Toyota has continued to see success on so many dimensions, where others struggle.
The Value Stream
In the perfect value stream, products are produced reliably, efficiently, with good quality, and in sufficient quantity at the individual process level and throughout the entire value stream. A suboptimal condition with respect to any of these characteristics constitutes a type of waste. Since no production value stream is perfect, all real-world process-manufacturing value streams will contain one or more of these wastes. These are targets of opportunity for any process-improvement effort.
LEAN SIX SIGMA TRAINING/CERTIFICATION
Intensive 25 Hrs Class Room training course leading to Lean Six Sigma Green Belt Certification, conducted by Real time consultants with 20 years expertise + online and class room support for six sigma project development upto 1 year...
Six Sigma Certificate
Register for the Course
Six Sigma training Feedback
Failure Mode and effect Analysis
What do we learn in the Lean program ?
Qualimations has a lean six sigma board that consists of senior lean six sigma consultants from several companies and expertise ranging from EPC,Healthcare,Automotive,Textile,Software and other sectors. This course is designed and continioulsy updated by them with latest methods and techniques... Read More
Lean Six Sigma Course

1st Sep to 1st Nov Black Belt Six Sigma, Online, WhatsApp: +91 98950 93119
E. : info@qualimations.com
Reg. Chennai: +91 9940622700
Reg.Online: Register for the Next Course